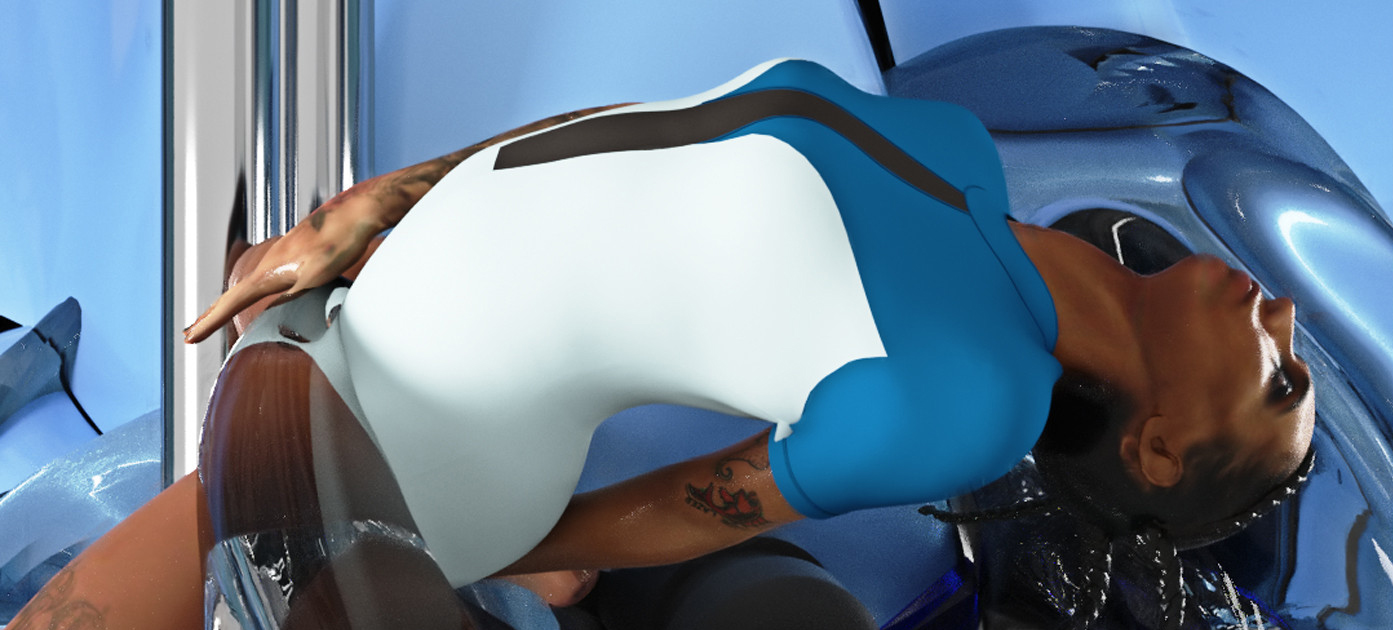
September 27, 2016 3D Modeling Chromat’s SS17 HYPERWAVE Collection for New York Fashion Week
At Body Labs, we’ve had the pleasure to work with many forward-thinking companies and teams. Many times, these collaborations have propelled industries in new directions not originally considered. In the fashion world, Chromat has been a leader not only empowering body positivity and diversity, but the role that technology plays in fashion as well. With the latter in mind, we had the opportunity to work with Chromat, Formlabs and Pussykrew to deliver a true 3D design, printing and animation pipeline centered around our body models.
With Chromat, our goal was to digitize dancer Mela Murder — wearing outfits from Chromat’s SS17 HYPERWAVE line — into a series of models optimized for 3D printing and animation during its New York Fashion Week events. Through this collaboration, we were able to explore the ways in which the 3D ecosystem could be leveraged throughout the fashion design, manufacturing and virtual try-on process. (View and download Mela’s 3D models on Sketchfab).
Digitizing a dancer
At the core of our technology is artificial intelligence (AI) — trained on all possible body shapes and poses — to produce the most accurate 3D digital body shape in the industry. Starting with this baseline understanding of human body shape, our technology is able to take very crude data sources — such as mobile scanning hardware or physical measurements — and transform them into accurate 3D body models.
This enabled us to use the Occipital Structure — a depth sensor attachment for the iPad Air 2 — to capture both depth and texture (color data) of dancer Mela Murder. From there, we were able to seamlessly process the depth data captured of Mela into an accurate 3D body model using our AI. After producing an accurate 3D model, we then reposed her and retargeted her texture from the original Structure scan onto her 3D model. Our AI-powered approach let us easily repose, measure and design within a 3D computer-aided design (CAD) program and animation software.
Creating 3D garments in CAD
Once we created Mela’s 3D model, her garments were then recreated digitally and draped on her reposed model using CAD (Clo3D). The digital garments could then be measured, sized and manufactured based off of Mela’s body measurements without tedious and time-consuming fittings or physical sample production. This method of design drastically cuts down on the design cycles and expensive iteration that takes place when producing physical samples.
Optimizing for 3D printing
Before creating and draping Mela’s models in 3D, we applied texture to her digital model, which was processed and made available for 3D printing and animation. The 3D models of Mela were then sent to Formlabs to be optimized for 3D printing. This was in preparation for Chromat’s SS17 HYPERWAVE runway show — where Formlabs’ Form 2 printers would be featured live printing our 3D models of Mela. In the near future, we imagine a manufacturing process that empowers designers to go from digital apparel design to 3D printing physical samples from the convenience of the studio. (Print-ready versions of our models can be accessed on Pinshape).
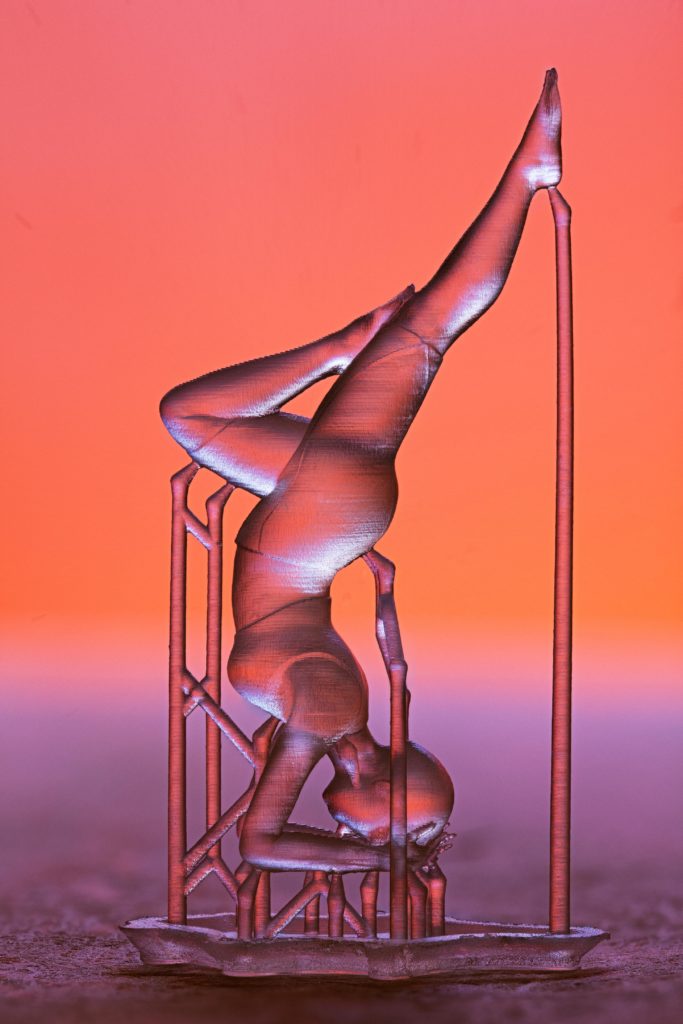
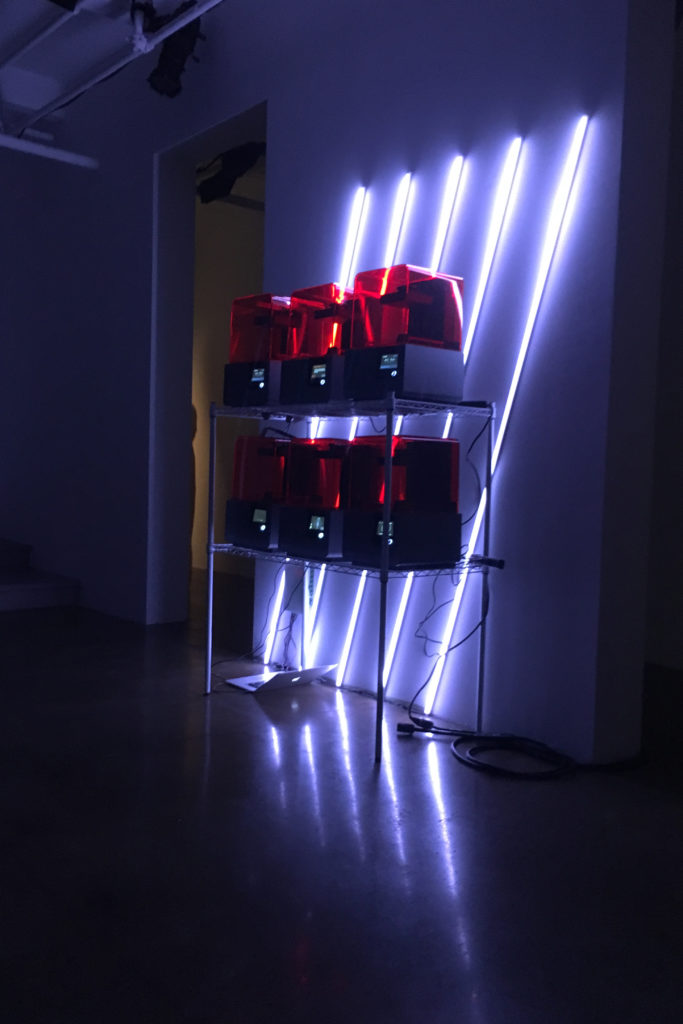
Preparing for 3D animation
Mela’s textured models were then sent to a group of animators (Pussykrew) to render within their amazing post-human digital environments for large-scale projection at the Tumblr Fashion Honors at Lightbox. Mela’s models had to be rigged with a skeleton to easily retarget her motion capture — which was recorded earlier by Pussykrew — onto her 3D model using Cinema 4D. From there, the projections were rendered in an astounding 8600 x 1200 pixel resolution at the event. Unlike fused and static 3D scans, our body models can be easily rigged and mocap can be realistically retargeted without labor-intensive sculpting of blend shapes.
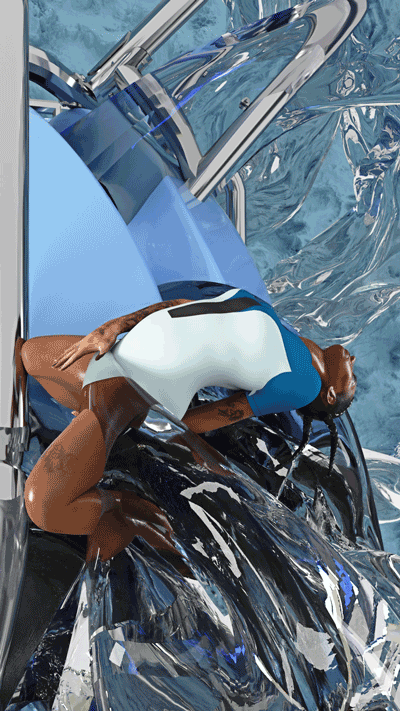

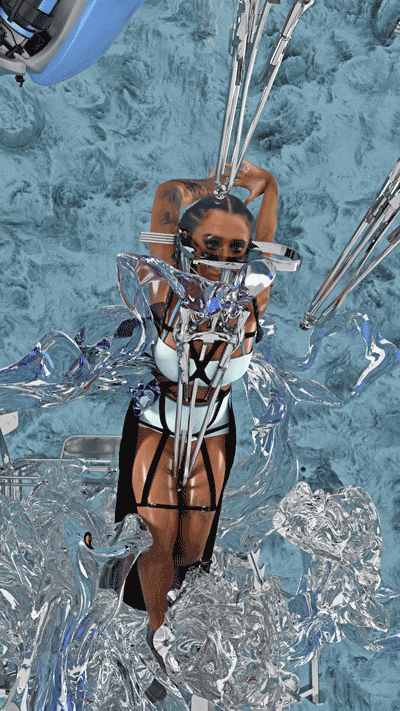
Wrapping Up
Amazing things happen when you can access accurate 3D digital body shape. It’s always been our goal at Body Labs to transform the human body into a digital platform upon and around which goods and services can be designed, produced, bought and sold. This project, alongside incredible partners, has enabled us to demonstrate to the fashion world what an effective 3D ecosystem can look like and how it can meaningfully impact your customers.